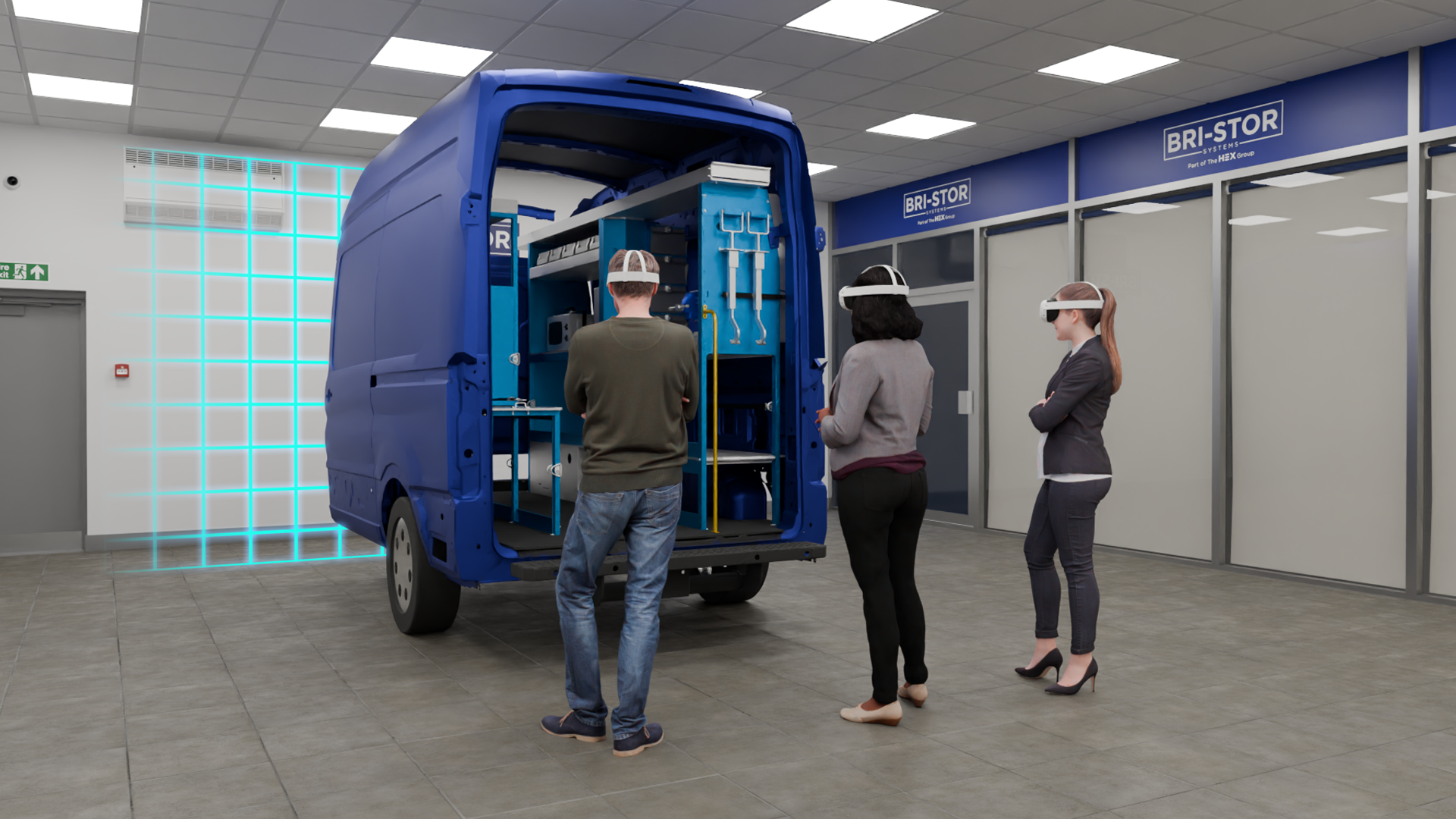
Challenge
Bri-Stor is a ‘one-stop shop’ for vehicle fleets, with up to 6,000 vehicles per customer. Their solutions include design, manufacture and installation of all fittings, which is done entirely in-house. Each fleet comprises a wide variety of vehicle models and specifications, each of which are treated from end-to-end as bespoke projects. With such customisation requirements comes added complexity.
Bri-Stor faces a significant risk when taking a design to production, with any design amendments having considerable impact on the efficiency of batch production, project delivery time and disrupting their manufacturing processes. Additionally, timing of production is vital to Bri-Stor; the quickest route to production is required to meet client delivery times and reduce the inherent impact of vehicle lease costs.
Approach
JoinXR was recommended to Bri-Stor as an excellent solution to solve their challenges. After an on-site visit, the JoinXR team was able to offer live demonstrations using Meta Quest 3 headsets and astutely outline Bri- Stor’s business needs and requirements. Bri-Stor’s engineering design team uses Solidworks for their CAD design – data from here (and many other CAD packages) can be smoothly pipelined into JoinXR.
JoinXR licences were rapidly deployed along with an end-user training allocation bespoke to solving Bri- Stor’s challenges. Implementation of XR has been supported by the JoinXR team with ongoing regular check-in meetings and training as required.
Solution
JoinXR is an excellent solution for Bri-Stor to manage its production risk. JoinXR offers Bri-Stor a means of both streamlining its product presentation to drive client engagement and to remove bottlenecks in CAD review workflows.
With JoinXR, Bri-Stor’s design engineers can rapidly convert their 3D files from Solidworks and also vehicle scan data and load them directly into JoinXR. From there, they can create a structured immersive presentation in minutes to explain and review their design in 3D. They can meet in headset directly with the client, removing the need for travel or any physical prototyping.
Using JoinXR, 3D models of vehicles can be shown at real-scale, proving ideal for reviewing internal fittings as in real life. Design amendments that are frequently missed on a 2D platform are quickly spotted and resolutions communicated and explained in real-time.
Getting started has been really easy, and the JoinXR team are always on hand to help with anything. In the first six months of using JoinXR, Bri-Stor reported their cost of travel on client visits and also the costs to produce samples for clients are reducing. This comes with the added benefit of greater engagement reported in their sales and prototyping processes with clients. The downstream benefits are that Bri-Stor can more efficiently manage their production risk. As they move forward further tangible improvements are on the horizon.